CAN FD Light: The New CAN Bus Engineers Wanted and the Industry Needed
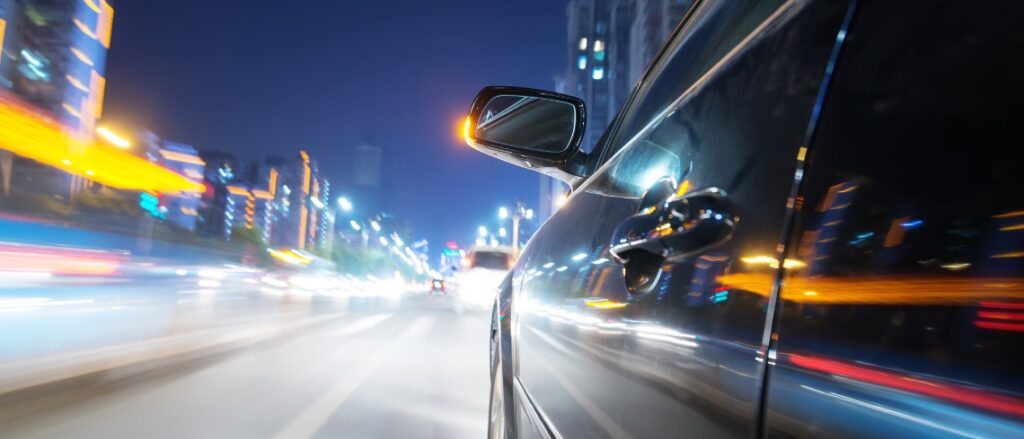
It’s rare when engineers can clearly anticipate the rise of a technology that will impact products for years to come, but this is exactly what we are witnessing with the rise of CAN FD Light. And the winners of tomorrow will be those who jumped on the bandwagon early. Hence, it’s essential to understand who should consider using this technology and why. A Controller Area Network (CAN) is a serial communication bus developed in the early 1980s by Bosch1. The technology satisfied the automotive industry’s unique requirements in ways no other protocol could at the time. Since then, CAN grew to address a lot more use cases. For instance, airport gates, construction equipment, or industrial applications all use the standard or its variant, CAN-FD.
CAN FD (Flexible Data-Rate) is a high-speed version of CAN designed to answer the need for greater bandwidth. The protocol holds 64 bytes per frame or eight times that of the first CAN standard. It also allows for faster transfers thanks to a dual bit-rate connection and increased reliability. However, as the number of sensors on an automotive grew, engineers realized that a “lighter” CAN FD protocol could offer tremendous technological and economic advantages. Hence, in 2020, the CAN in Automation (CiA) organization announced the creation of CAN FD Light. To learn more about it, we sat down with Fred Rennig, System Engineer for Automotive Networking and Network Security at ST, and Chairman of the CAN FD Light Special Interest Group.
Knowing the Signs and Anticipating the Trends
Before delving into the standard itself, Fred shone a light on the industry’s enthusiasm around CAN FD Light. Indeed, a few companies are already working with it, even before its standardization. ST, Audi, and OLEDWorks recently showed a rear-lighting demo that used the protocol. European and Japanese carmakers expressed positive feedback, and makers of CAN analyzing or measurement equipment are also showing interest. Obviously, many are still waiting for an official standard before fully committing to it. However, a working draft is under examination, and a standard should be ready by 2021. Hence, the issue is no longer if but when industries will adopt CAN FD Light. As a result, engineers must familiarize themselves with the standard to ensure they are not left behind. Hence, let us tackle three misconceptions that may stop teams from jumping on the bandwagon early.
1. CAN FD Light Isn’t Just Like CAN FD, It Uses a New Commander-Responder Architecture
Moving Away From Multi-Commander Topology
The “CAN FD Light” serial communication bus is far more than a stripped-down version of CAN FD but a new architecture. While CAN or CAN FD use a multi-commander topology, CAN FD Light relies on a commander-responder architecture. In a multi-commander setup, all units (rear lighting, sensors, infotainment, etc.) require a module with its microcontroller, power supply, and more. Moreover, the network must connect all modules with each other and with the central controller. The commander-responder topology of CAN FD Light is simpler because the main controller now directly commands each unit. As microcontrollers get increasingly more powerful, the need for an intermediary module is obsolete, enabling more straightforward communications.
Simpler Than CAN FD but Just as Robust
Engineers, especially those with experience in CAN or CAN FD, will need to adjust since modules no longer require arbitration. The commander, meaning the main controller, simply sends data to a specific unit, which will then send its information back if necessary. One reason CAN FD Light is rapidly becoming popular is because some engineers were already using CAN FD in this way. Despite its interconnectivity, some relied heavily on the main domain, even if CAN FD was not designed with this purpose in mind. However, the new protocol natively revolves around this simpler behavior, giving those engineers the system they were looking for. Additionally, CAN FD Light also benefits from the same robustness and safety features as CAN FD. For instance, CAN FD Light inherited CAN FD’s 64-bit data frame with cyclic-redundancy-check (CRC).
2. CAN FD Light Isn’t Just Simpler, It Increases Efficiencies
The Technological Effectiveness
Too often, engineers underestimate the impact of the commander-responder topology on the overall design. Besides arbitration being obsolete, the system no longer needs error frames over the network to ensure consistency. In fact, CAN FD Light has such a straightforward approach that it is possible to implement it as a pure hardware solution. Indeed, traditionally, the software inside the domain controller manages the various modules. When a CAN or CAN FD system connects different complex modules, the software enables more flexibility. However, engineers do not need it when dealing with simpler systems like environmental sensors or rear lighting. Hence, CAN FD Light is a significant advancement that ensures teams no longer need to write complex software systems to manage simple units.
The Cost-Effectiveness
Another vital advantage of CAN FD Light is its cost-effectiveness. Many companies are already experimenting with it because removing a control module between a unit and the main controller offers substantial savings. For instance, it vastly reduces the number of microcontrollers necessary. Similarly, a pure hardware implementation cuts down on software development costs. Furthermore, companies no longer need highly accurate ceramic resonators or crystal oscillators. Indeed, the multi-commander topology of CAN demands that each bus be exact to synchronize all messages. Most car manufacturers require a clock accuracy below 0.1%, which in turn demands expensive external crystals. Such devices can make up as much as half the price of an actuator unit. In CAN FD Light’s commander-responder system, the responder’s internal clock is sufficient since the main controller is the only one initiating communication.
3. CAN FD Light Licenses Are Not Less Accessible, They Use the Same Channels as Other CAN Protocols
Some engineers may be reluctant to adopt CAN FD Light for fear that its licensing structure may involve different companies. However, the fact that the protocol is an evolution of CAN FD means that the process for obtaining a license is identical to the other CAN standards. Companies will use the same channels for a CAN, CAN FD, or CAN FD Light license. As a result, companies already familiar with the process can easily obtain the rights to the new technology and rapidly implement it. Hence, as the industry nears the standardization of CAN FD Light, having a low barrier to entry to such a straightforward technology easily explains why we expect a rapid market penetration.
Click Link- https://blog.st.com/can-fd-light/